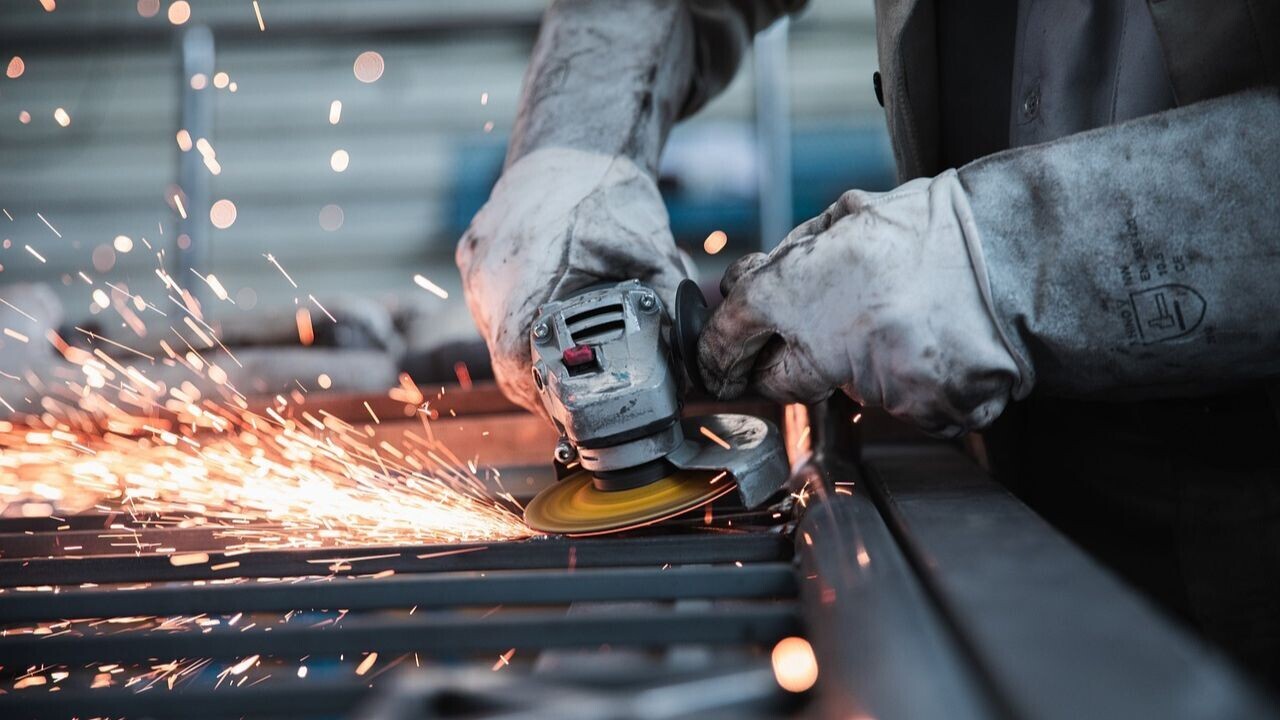
Researchers from the University of Birmingham have developed an innovative method for existing furnaces that could reduce steelmaking’s CO2 emission by nearly 90%.
The iron and steel industry is a major cause of greenhouse gasses, accounting for 9% of global emissions. That’s because of the inherent carbon-intensive nature of steel production in blast furnaces, which currently represent the most-widely used practice.
In blast furnace steel manufacturing, coke (a type of coal) is used to produce metallic iron from ore obtained from mining — which releases large quantities of carbon dioxide in the process. According to Dr Harriet Kildahl, who co-devised the method with Professor Yulong Ding, their technology aims to convert this carbon dioxide into carbon monoxide that can be reused in the iron ore reaction.
This is realised using a thermochemical cycle which performs chemical reactions through changes in temperature. That way, the typically damaging CO2 is turned into a useful part of the reaction, forming “an almost perfect closed carbon loop.” This drastically reduces emission by the amount of coke needed and, subsequently, lowers steelmaking’s emissions by up to 88%.
As per the researchers, if this method was implemented in the remaining two blast furnaces in the UK, it could save £1.28 billion in 5 years, all while reducing the country’s overall emissions by 2.9%.
“Current proposals for decarbonising the steel sector rely on phasing out existing plants and introducing electric arc furnaces powered by renewable electricity. However, an electric arc furnace plant can cost over £1 billion to build, which makes this switch economically unfeasible in the time remaining to meet the Paris Climate Agreement,” Professor Ding said. “The system we are proposing can be retrofitted to existing plants, which reduces the risk of stranded assets, and both the reduction in CO2, and the cost savings, are seen immediately.”
University of Birmingham Enterprise has filed a patent application covering the system and its use in metal production. It’s currently looking for partners to take part in pilot studies and deliver this technology to existing infrastructure, or collaborate on further research to develop the process.
You read the full study here.
Get the TNW newsletter
Get the most important tech news in your inbox each week.