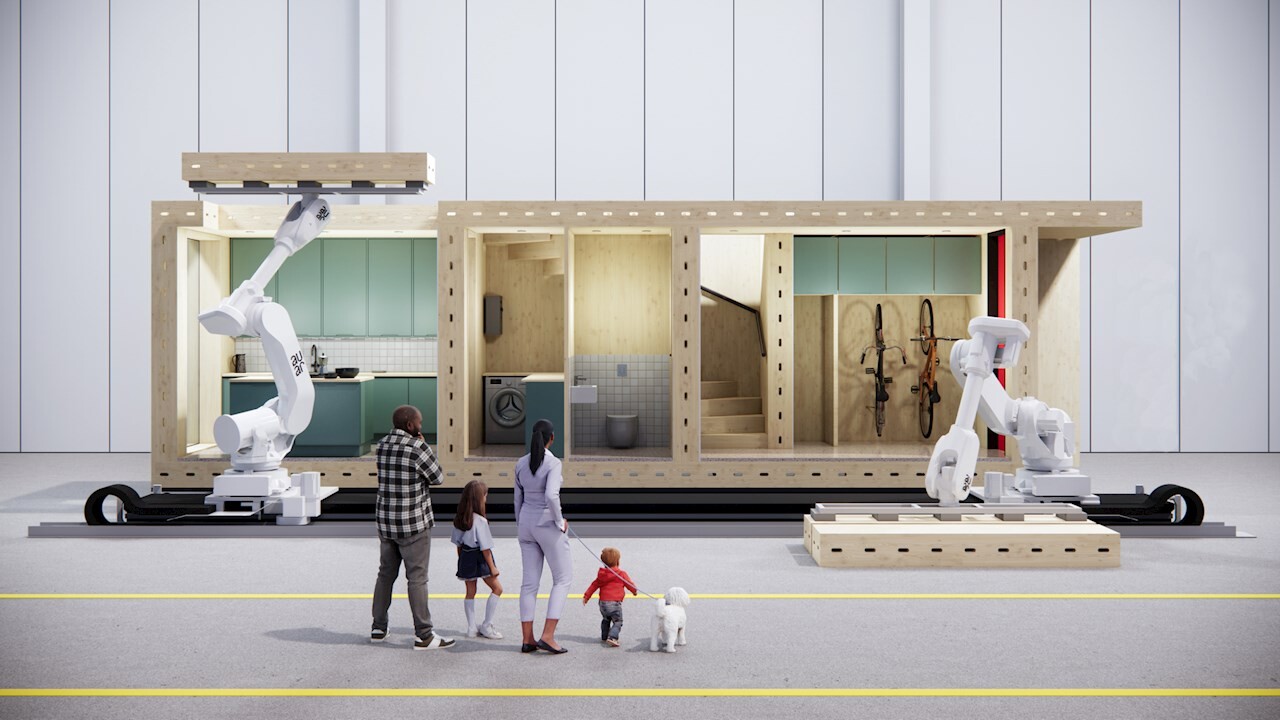
From the outside, it looks like a clean, modern social housing block. You can tell it’s new — there are 84 shiny solar panels on the roof and the fresh paint has barely dried on the walls. But it’s how this 56-dwelling building in Barcelona, complete with ground floor nursery, was designed and built that really matters.
“Our software is our superpower,” says Lucas Carné, co-founder of 011h, a construction tech firm, as he describes how his company has designed digital tools to help architects plan buildings like this one. “We use a lot of prefab,” he adds. “That reduces the need for on-site labour.”
Prefabricated construction relies on factory-made parts or components of buildings that are joined together on-site. It is far from a new concept but 011h has tried to make it much easier for architects to use this approach. The firm offers architectural software plugins containing libraries full of these prefab components. It makes the process of designing a building a bit like playing with digital Lego.
Improving productivity to solve housing shortage
So far, 011h has collaborated with architectural and construction firms on several Spanish apartment blocks of differing designs — roughly completing one such block per year. The company is now planning to scale up to multiple projects annually, encompassing a total of around 200 dwellings per year. The firm has raised more than 35 million euros to date and has 90 employees.
This push to streamline design and construction is sorely needed, suggests Carné. As in many European countries, demand for housing in Spain is currently outpacing supply. Across the continent, the picture varies but a lack of housing, and a shortage of construction workers, are common themes. Materials costs also rocketed during the worst years of the pandemic. Now, various European startups are coming up with a raft of ideas to try and mitigate these problems.
“Our goal is to improve productivity,” says Carné. “Probably the biggest problem this industry is facing is that productivity is stagnant.”
Build with digital Lego
Traditionally, construction is a woefully disjointed business. Roughly speaking, an architect will come up with a design and then hand it to a builder who, separately, will work out how to put that design together, for real. 011h takes a different stance. “We run a design and build process together with the suppliers and solutions we are going to use,” says Carné.
All the information about who will supply each building part, the costs involved, and the carbon footprint is collated from the very start in the company’s software. His team focuses on using sustainable materials — responsibly sourced timber rather than concrete, for instance, since the latter is high in embodied carbon.
011h’s buildings have achieved embodied carbon emissions lower than 400 kg of CO2 equivalent per square metre — significantly better than current averages. Plus, construction time is also shortened, by around 30% versus the average, claims Carné.
Construction conservatism can hinder new technology adoption
Revolutionising construction with digital technology has promise but it is difficult to do, says Sam O’Gorman at McKinsey’s Real Estate practice. There is often resistance to new ways of doing things in the construction sector, he notes. Plus, given the large amount of capital involved, there is significant risk if a project goes awry: “One mess-up could cost the business.”
However, if firms entering this space can establish a good track record — perhaps through significant self-funding, at least initially — then they might be able to convince potential partners that they are worthy of collaboration or investment, adds O’Gorman.
Another company that says technology can help us build homes smarter and faster is AUAR (Automated Architecture), in the UK. Gilles Retsin, co-founder and CTO, says his firm’s approach is to supply building firms with “micro-factories” — boxes with big robot arms inside. These arms work tirelessly to produce modular building units. Imagine a roughly 4×3 metre timber floor or wall panel, thick enough to be filled with insulation, which can be joined together with other panels to make a building.
A bot job
“The robot will essentially grip raw materials, cut them, and put them on an assembly table where it nails them together,” explains Retsin. “Then they’re craned onto site by humans.” AUAR has 17 employees and has raised £2.6 million.
The company is currently targeting the European and US markets, both of which are suffering from labour shortages in the construction sector. “We just built a two-storey building in Belgium,” says Retsin. In that case, the microfactory robot took about three days to make the building block units and human workers took a further three days to connect those units together and complete the building’s main structure.
Initially, AUAR provided its microfactory robots at a cost of £250,000 each but Retsin says the firm is shifting to a hardware-as-a-service model in which builders can pay a smaller fee to have the microfactory delivered to site. They will then pay a further small charge per square metre of building produced.
Although the firm is yet to scale, Retsin emphasises the huge potential of running the robot arms continuously — and perhaps using many of them in parallel. “The capacity of one robot is 200 homes per year, if you run it eight hours per day,” he says, adding that the next step for the firm is to tackle a 30-home project in the US next year.
Robo brickie
Finally, even in 2024, bricklaying remains a crucial skill required for housebuilding in Europe, as brick-based construction remains prized by European homebuyers. However, bricklayers are among the workers currently in very short supply. Monumental, based in Amsterdam, has an alternative.
“You tell me, ‘I want to build a façade for a house, it’s X square metres’,” says Salar al Khafaji, founder and CEO. “I will quote you a price and do it for you — but I will do it with robots.”
The firm, which has raised $25 million to date and has 32 employees, offers bots capable of laying mortar and bricks in a careful sequence in order to build a wall automatically.
The process involves three individual robots, which each take on a separate task: either supplying a brick, laying a blob of mortar, or putting a brick in place. Pointing, however — neatly finishing the exposed mortar joints visible between bricks — still has to be done manually.
In videos like the one above, the bricklaying carried out by the robots seems rather slow but al Khafaji stresses that because the machine is able to keep working continuously without breaks, it is able to roughly match the average human bricklayer’s rate of 500 bricks laid per day.
Human in the loop still very much required
Automating specific activities such as this that can slot into traditional construction processes could help these technologies get adopted sooner, suggests O’Gorman. Though he notes that human oversight and finishing of tasks is still required. It may be a long time before we see robot builders working through the night with little or no supervision.
Still, Monumental’s robots have already helped to build among other things a canal retaining wall in Amsterdam and a one-storey villa. Demand is encouraging, says al Khafaji, indicating that he has orders for several new terraced houses on the books for the coming months. The firm is also exploring the potential of using more environmentally friendly bricks, since standard clay bricks contain a high amount of embodied carbon.
While Monumental’s bricklaying machines can’t yet place bricks standing vertically, or build arches, they can do curved corners and also lay bricks in artistic indented patterns.
“That’s really exciting to me,” says al Khafaji, “That gets beauty back into our built environment.”
Get the TNW newsletter
Get the most important tech news in your inbox each week.