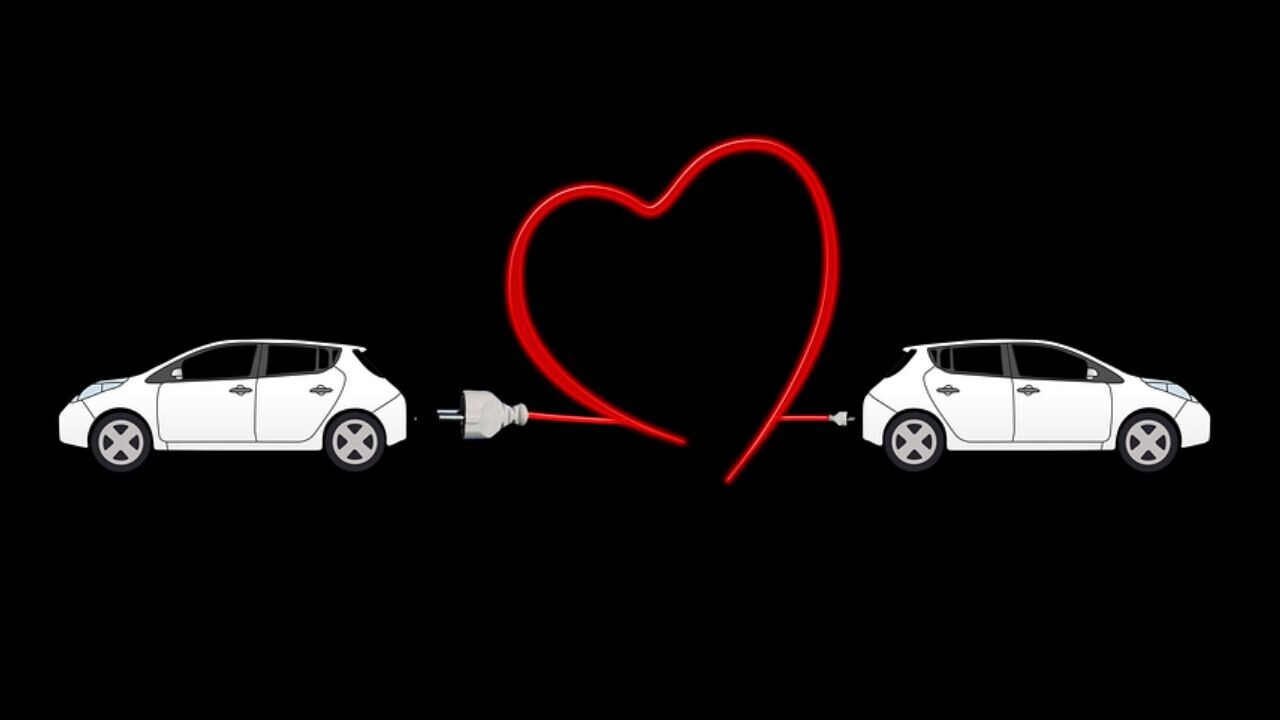
With more and more EVs on the road, the need for battery recycling and reuse has emerged as a necessity to further enhance the sustainability of these vehicles. But there’s another component whose potential for a second life could be a game changer: the electric motor.
Extending the use phase of electric motors is crucial for two reasons. Firstly, they contain valuable raw materials such as copper and rare earth metals such as neodymium, which can’t be easily recovered. Secondly, the raw materials used for the motors have a larger carbon footprint than those used for a combustion engine.
Current recycling methods have proven insufficient in addressing these issues. The recycled raw materials are often contaminated and can’t be reused for motor applications, while other individual components of the electric motor are destroyed.
To help tackle this challenge, researchers from the Fraunhofer Institute for Manufacturing Engineering and Automation IPA have launched the REASSERT project.
“We want to establish a closed-loop system in which valuable resources are reused in order to eliminate dependency on raw material imports and to minimise raw material extraction,” said Julian Große Erdmann, scientist at the Institute.
With this aim at its core, the project focuses on four value retention strategies: reuse of the entire engine; repair with the replacement of of defective components; remanufacturing, where all components are disassembled, cleaned, conditioned, and reassembled; and raw material recycling by disassembling the motor and sorting the individual materials before shedding.
A new process chain
The project will establish a complete process, from motor classification to disassembly, component diagnosis, reassembly, and end-of-life testing. Each of the steps included will have its own demonstrator and test rig.
“Depending on the chosen value preservation strategy, different process steps and chains are involved, so the effort for reconditioning may vary,” explained Große Erdmann.
The team will use reference motors from the passenger EV segment and leverage a specially-developed AI tool that helps select the optimal value retention strategy for each motor.
REASSERT’s goal is to develop a prototype motor that enables the effortless application of the four value retention strategies. If successful, this could lead to the design of new electric motors that support a circular economy.
The project also involves five industry partners: Schaeffler (as consortium leader), the Karlsruhe Institute of Technology, BRIGHT Testing GmbH, iFAKT GmbH and Riebesam GmbH & Co. KG. It has secured funding by the German Federal Ministry for Economic Affairs and Climate Action.
Get the TNW newsletter
Get the most important tech news in your inbox each week.